고장모드 영향분석 FMEA를 통한 개선 참인자(Vital few) 찾기
식스시그마(Six Sigma) 개선 기법에서 고장모드 영향분석(FMEA)은 문제를일으키는 참인자를 도출하여 분석 및 실험계획을 수립하기 위한 개선 우선순위를 명확히 하는데 유용한 프로세스로 활용되고 있습니다.
현장의 문제를 개선하기 위해서는 우선 3현주의 사상으로 현장에서 문제점을 발견할 줄 알고 그 문제점에 대한 개선대책을 수립하고 개선을 실시하며 실시후 프로세스 모니터링을 통한 유효성 검증을 실시 하여야하고 이러한 개선 프로세스를 알고 실행할 수 있어야 합니다.
현장 개선에 있어 무엇보다 많은 문제점들 중 실질적이고 가장 큰 영향이 미치는 참인자(Vital few)를 찾아 개선을 위한 분석이나 개선실행의 우선순위를 명확히 하는 것이 개선활동의 지름길이 될 것입니다.
참인자를 도출하기 위해 프로세스맵,파레토분석,브레인스초밍,특성요인도 등 많은 분석을 하고 문제를 일으키는 각 팩터에 대한 FDM등을 실행하는 것도 중요한 개선 프로세스라고 할 것입니다.
이 번 작성글은 개선 프로세스에 있어 고장모드 영향분석, FMEA(Failure Modes and Effects Analysis)을 통한 프로세스별 고장모드에 대한 영향분석을 통해 프로세스에 대한 심각도 발생도,검출도를 평가하여 개선 참인자를 도출하여 우선순위를 명확히 하는 방법을 알아볼 것입니다.
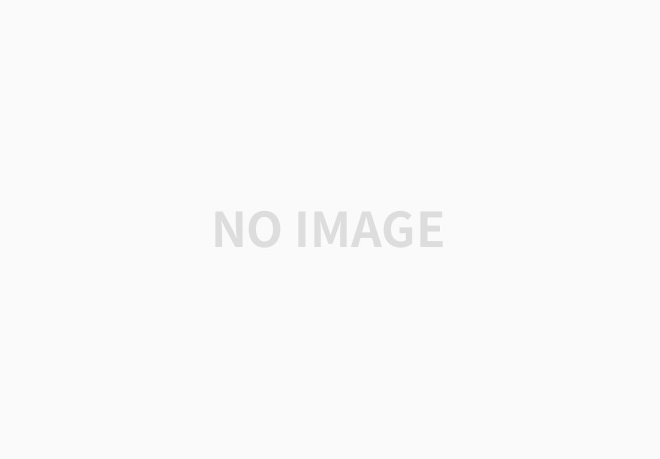
1. 고장모드 영향분석(FMEA) 란?
고장모드 영향분석은 제품 또는 프로세스의 잠재적인 고장과 그 영향을 찾아내고 평가하는 것으로 잠재적 고장의 발생 기회를 제거하거나 감소시킬 수 있는 조치 식별,프로세스의 문서화를 말합니다.
고장모드 영향분석(FMEA)의 종류는 시스템이나 초기 설계단계에서 시행하는 최상위 수준의 시스템 FMEA, 제품 설계에 관련된 고장을 식별 및 방지하기 위해 시행하는 설계 FMEA, 제조 또는 기타 프로세스에 대한 고장의 식별 및 방지를 위한 FMEA 등으로 구분할 수 있습니다.
2. 프로세스 FMEA
(1) 프로세스 FMEA의 내용
공정이나 제품이 고객의 주요 요구사항에 맞출 수 없게 되는 원인을 확인하는 세부 문서로 실패 가능 요인을 종합한 실질적 문서이고 궁극적으로 모든 프로세스를 포함하는 것입니다.
(2) 프로세스 FMEA의 용도
잠재인자로 인한 제품이나 공정의 실패를 확인하고 실패를 예방하기 위한 계획 문서로 활용하며 관리계획의 항목을 작성하는 기초 자료로 활용,프로세스 개선에 필요한 조치의 추적과 우선순위 파악에 활용됩니다.
(3) 프로세스 FMEA의 목적
새로운 공정의 분석을 돕고 공정관리 계획의 결함 식별 가능,행동의 우선순위 결정을 하고 공정변경에 다른 위험 평가,향후 고려할 잠재적 변수의 식별,공정 설계 엔지니어들로 하여금 현재 공정의 약점을 이해하고 새로운 제조 공정의 개발을 할 때 참고자료로 활용됩니다
(4) 고장모드의 종류
- 설계상의 결함 - 설계원리에 고유한 성질이라 보여질 수 있는 결함,도면의 부재,누갈 등
- 제조상의 결함 - 가공법의 결하,조립실수
- 품질관리상의 결함 - 검사 불충분 또는 실수,공정관리의 부적절
- 사용상의 결함 - 잘못된 조작,설계조검과 다른 패턴에서 사용
- 보전상의 결함 - 보전작업실수,보전메뉴얼 부재
(5)고장모드 원인과 관리방법
고장모드의 원인으로는 고장모드의 발생을 야기하는 공정 변동의 원인을 규명하여 치명도가 높은 고장모드에 대해 우선권을 부여합니다.
고자오드 관리방법으로 고장모드 및 원인 규명 그리고 고장을 사전에 예방하기 위한 체계적 방법으로는 예방 단계에서 Fool Proof설계,Fail Safe설계 등이 있고 관리 단계에서 감사,체크리스트,검사,실험실 시험,훈련,PM활동 등이 있습니다.
3. 프로세스 FMEA 시트 작성
고장모드 영향분석(FMEA)시트 작성시 우선 프로젝트에 대한 FMEA NO,FMEA유형,공정책임자,작성자,관련제품,작성일,프로젝트 팀원명단 등 기본사항을 기록하고작성합니다.
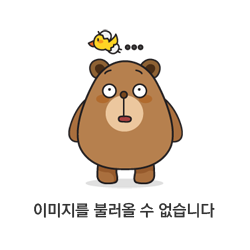
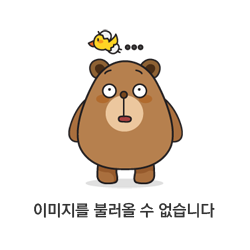
프로세스 단계를 간단하게 기록하고 여러 기능이 있을 경우 따로 분리하여 기록합니다
잠재적 고장모드는 실제 작업환경(온도,습도,먼지,진동 등)하에서 발생할 수 있는 모든 자재적인 고장 모드를 기록합니다.
잠재적 영향으로 내부고객 또는 외부 고객에 의해 인식되는 영향 정도오 안전 또는 법적 규제 조항에 저촉될 위험 등을 기록합니다.
심각도는 잠재적 영향의 심각도를 말하며 각 고장 모드는 오직 하나의 심각도 등급을 가지며 가장 심각한 영햐의 심각도 등급을 기록합니다.
심각도 등급은 다음과 같이 분류합니다.
- 10점 - 안전 또는 정부 규제 조항에 예고 없이 저촉
- 9점 - 안전 또는 정부 규제 조항에 예고와 함께 저촉
- 8점 - 주 기능의 수행불가
- 7점 - 주 기능의 제한적 수행,고객불만
- 6점 - 편의 기능 수행불가
- 5점 - 편의 기능 제한적 수행
- 4점 - 대부분 고객이 감지할 수 있는 결함
- 3점 - 보통의 고객이 rka지할 수 있는 결함
- 2점 - 까다로운 고객이 감지할 수 있는 결함
- 1점 - None
잠재적 원인 및 고장 메카니즘을 기입 하는 것은 취약점,잠재적 고장 모두의 원인이될 가능성이 있는 것을 기록하고 무엇을,왜?의 반복을 통해 근본 원인규명 기록하며 근본 원인 규명을 위해 특성요인도나 기타 분석 자료를 첨부할 수 있습니다
발생도 기록 점수는 아래와 같이 분류합니다.
- 10점 - 2중 1이상(고장을 거의 피할 수 없슴)
- 9점 - 3중 1
- 8점 - 8중 1(반복된 고장)
- 7점- 20중 1
- 6점 - 80중 1
- 5점 - 400중 1(간혹고장)
- 4점 - 2,000중 1
- 3점 - 15,000중 1(비교적 고장이 없슴)
- 2점 - 150,000중1
- 1점 - 1,500,000중 1이하(발생가능성 거의없슴)
현재 프로세스 관리상태의 기록은 잠재적 고장 모드의 원인을 제거하기 위한 현재의 관리사항,예방조치 사항,수정을 위해 원인을 규명하는 일,고장 모드 자체를 탐지하는 행위 등을 기록합니다.
고장원인 및 수반되는 고장탐지의 가능성 기준으로 검출도 기입 등급을 아래와 같이 분류합니다.
- 10점 - 장원인 및 수반되는 고장 탐지 불가
- 9점 - 고장 탐지의 매우 희박한 가능성
- 8점 - 고장 탐지의 희박한 가능성
- 7점 - 고장 탐지의 매우 낮은 가능성
- 6점 - 고장 탐지의 낮은 가능성
- 5점 - 고장 탐지의 보통정도 가능성
- 4점 - 고장 탐지의 보통보다 높은 가능성
- 3점 - 고장탐지의 높은 가능성
- 2점 - 고장탐지의 매우 높은 가능성
- 1점 - 고장을 거의 확실하게 탐지
RPN(Risk Priority Number)기록
- RPN = 심각도*발생도*검출도
- RPN이 높은 고장 모드의 제거에 집중
- RPN이 높지 않더라도 심각도가 큰 고장 모드에 대해서는 특별한 주의가 요구
RPN 값이 100이상의 것이나 고장발생도,심각도,검출도 평가 등급이 8 이상의 경우 개선대책 수립 및 실시하고 FMEA의 해당 항목에 중요 표시를 하며 개선대책이 필요 없을 시는 그 해당 항목에서 개선 필요없슴 등으로 표시해 둡니다.
이제 프로세스맵,특성요인도,FDM,FMEA 등을 통해 상품이나 제품에 문제를 일으키는 참인자를 찾아 내었으니 우선수위를 정하여 리스트업하고 각 인자들에 대한 유의수준 등을 확인하기 위해 신뢰성 있는 데이터를 수집하고 분석을 실행합니다.
분석,개선 단계에 대해 차후에 글을 정리 하길 하고 FMEA 고장모드 영향분석 방법에 대한 글을 마칩니다.
고장모드 영향분석(FMEA)를 공부하는 경우이든 현장에서 개선의 툴을 찾는 경우이든 조금이라도 도움이 되었으면 하는 바입니다.
고장모드 영향분석(FMEA)을 실행하기 이전 유용한 분석 프로세스인 QC 7가지 도구에 대해 정리글 링크해 두니 함게 보면 도움이 될 것입니다